Steps Involved in Steel Fabrication
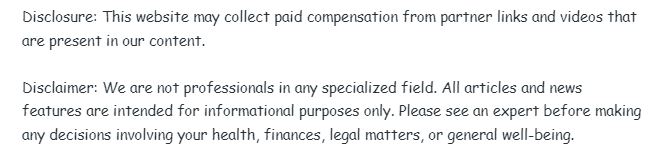
Steel fabrication is a critical process used in many industries, from construction and automotive to aerospace and manufacturing. It involves shaping, cutting and assembling steel into a wide range of products, from structural beams and supports to custom-made components.
The process requires skilled craftsmanship, precision and a variety of tools to achieve the desired outcome. In this article, we will explore the key steps involved in steel fabrication, highlighting the importance of each stage to ensure a successful project.
1. Design and Planning
The first and most crucial step in steel fabrication is designing and planning. The fabrication process begins with a detailed design that specifies the dimensions, materials and overall layout of the project. Engineers and designers work closely with clients to ensure that the steel fabrication project meets the required specifications and industry standards.
2. Material Selection
Once the design is finalised, the next step is selecting the appropriate steel material for the project. Steel comes in various grades, each with its unique properties such as strength, flexibility and corrosion resistance. The choice of material depends on the specific requirements of the project, such as the intended use, environmental conditions and load-bearing capacity.
3. Cutting
Once the materials have been selected, the next step in the steel fabrication process is cutting. Steel needs to be cut into the required shapes and sizes to fit the project’s design. There are various methods of cutting steel, including:
- Oxy-Acetylene Cutting: This method uses a combination of oxygen and acetylene gas to cut through steel by heating the material to its melting point.
- Plasma Cutting: Plasma cutting uses a high-velocity jet of ionised gas to cut through steel. It is a fast and precise method, ideal for thicker pieces of steel.
- Laser Cutting: For intricate designs and high precision, laser cutting is used. It utilises a focused laser beam to melt or vaporise the steel at the cutting point.
- Water Jet Cutting: Water jet cutting uses a high-pressure stream of water mixed with abrasive particles to cut through steel. This method is ideal for materials that might be sensitive to heat.
The cutting process must be done with precision to ensure that the steel pieces fit together correctly during assembly. High-quality cutting tools and techniques are essential to achieving the necessary accuracy.
4. Bending and Forming
After cutting, the next step is bending and forming the steel into the desired shape. This is typically done using machines such as press brakes or rollers. The goal is to manipulate the steel into the required angles, curves, and shapes that will fit together as per the design specifications.
5. Welding
Welding is a vital step in steel fabrication, as it involves joining two or more pieces of steel together to form a complete structure or component. There are several welding methods used in steel fabrication, including:
- MIG Welding (Metal Inert Gas): MIG welding is a popular method for welding steel. It uses a continuously fed wire as the electrode, and an inert gas is used to protect the weld from contamination.
- TIG Welding (Tungsten Inert Gas): TIG welding is used for more precise and clean welds. It uses a non-consumable tungsten electrode to create the weld.
- Stick Welding (Shielded Metal Arc Welding): Stick welding is a versatile and durable method used for welding thicker materials. It is often used in construction and industrial applications.
The welding process requires expertise to ensure that the joints are strong, durable and meet the required specifications. Properly welded joints are critical for the safety and longevity of the final product.
6. Finishing
After welding, the steel components may require finishing processes to improve their appearance, smoothness and resistance to corrosion. Some common finishing processes in steel fabrication include:
- Grinding: Grinding is used to smooth out rough edges, remove welding spatter or level surfaces.
- Polishing: Polishing is done to create a smooth, shiny surface on the steel, especially for decorative or high-visibility components.
- Sandblasting: Sandblasting involves blasting the steel surface with abrasive materials to clean and prepare it for coating or painting.
- Coating: Steel components are often coated with protective layers to prevent rust and corrosion. Common coatings include galvanising (zinc coating), powder coating, or painting.
The finishing process ensures that the fabricated steel components are not only functional but also aesthetically pleasing and resistant to wear and tear.
7. Assembly and Installation
The final step in the steel fabrication process is assembly and installation. After the individual pieces are fabricated, they are brought together to form the final structure. This may involve bolting, welding or riveting the steel components together, depending on the design.
Steel fabrication is a complex and multi-step process that requires skill, precision and careful planning. From the initial design and material selection to the cutting, welding and finishing stages, each step plays a crucial role in ensuring the final product meets the required standards. Steel fabrication is used in a wide range of industries, and its versatility makes it an essential part of modern construction and manufacturing. By understanding the steps involved in steel fabrication, you can better appreciate the intricacies of this craft and the work required to create strong, durable steel structures.
.